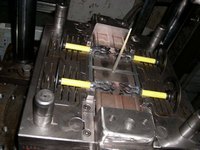
Insert Molded
Rebar Chair
|
Home /
Casting /
Die Casting
Die casting is a
process in which molten metal is forced under high pressure into
molds allowing for each part to be made identical to
the mold. Die casting is especially suited for metal products where a
large quantity of parts are needed with fine detail, a good surface finish,
dimensional consistency and cost savings over other processes.
The pressure and use of molds made from high grade heat hardened tooling
steel allows for manufacturing of walls thinner than
what other processes could make while at the same time keeping steady the
structural integrity and strength of the product.
More often than
not, metal is no longer required as exotic plastic materials are available
and plastic more often than not is a better
substitute. So long
as intense strength or hardness is not required,
injection molding can provide a less expensive, faster, and just as good alternative.
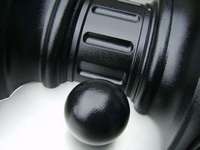 |
 |
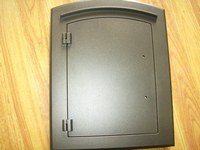 |
Die Cast
Mailbox Stand Cover with Ball Accessory , Powder Coated Black |
Die Cast
Multi-User Storage Unit Top Cover, Powder Coated Black |
Die Cast Individual
Mailbox Frame, Cover and Hinges, Powder Coated Bronze |
Sand Casting
Sand casting uses
the same principles as die casting, in which molten metal is put into a
cavity allowing the product to form as according to the mold its made from.
A pattern is inserted into the sand leaving an empty cavity in which the
product is cast from. However, as the mold is made from a sand
mixture, the surface detail, dimensional accuracy and uniformity can never
be as good as die casting. On the plus side, the molds are
substantially cheaper leading to less startup capital needed, but they do
lead to higher labor costs. This makes die casting cost less in the
long run for medium to large volume products.
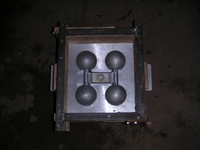 |
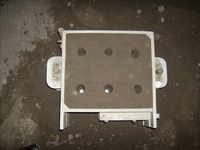 |
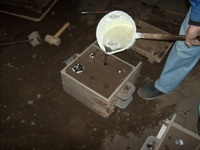 |
The
pattern is inserted into the sand creating empty cavities. |
Once the
pattern is removed, the mold is ready for production. |
Molten
metal is poured into the empty cavities of the mold forming the parts. |
|
|