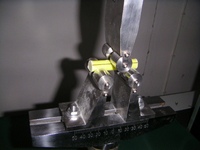
In-House Testing:
Short Beam Shear
Testing |
Home /
Injection Molding
/
Plastics
3c interglobal ltd has both experience
and proficiency in the following manufacturing practices with regard to
plastics. Our capabilities include the ability to do Injection Molding, Insert
Molding, Over Molding, Blow Molding as well as Extrusion. Read further
to understand the differences in each type or contact us and we will be
What plastic is right for me?
We will analyze
your product for the required physical and mechanical properties to choose
an accurate material for your product. Common requirements often
include high strength, temperature resistance, weather resistance, or extra
high precision.
We have experience
with regards to plastic product manufacturing in materials ranging from common
resins to engineered resins (fairly exotic). We have previously manufactured using
plastics from the families of PP, PE, PVC, ABS, AS (SAN), Acetyl, Nylon,
to name just a few. We use materials from world class manufacturers like Dupont,
LG, BASF, Sinopec, Ciba and so on or the lower end depending on what
kind of budget you have for your product and the requirements of the product. Some specialized injection
molded plastic parts may require reinforcement with glass or carbon fibers
imbedded in the resin.
Our experts in plastic coloration can choose pigments to give your product
the desired color. We custom match the color required and have a
master batch created so that all products are consistently the same color
throughout the life of the product. Often, ultraviolet inhibitors can be added to
protect the product against color fading as well as protecting for a weakening of strength
from sunlight.
Injection Molding
Many of the
high-tolerance plastic components on the market today are injection molded.
Using a steel mold, melted plastic is injected into the mold forming
the shape and critical dimensions required of it. Designing parts that
has the required physical properties and also the tight tolerances for
proper assembly is always a complex process. We keep these manufacturing
points in mind during the design phase so that we produce exactly what you
need.
A good design is
critical and crucial to enabling mass-production and
cost-savings.
Tight tolerances
and difficult configurations are our area of expertise. They are common challenges
in injection molding and are easily overcome
by our experienced design and engineering team.
Understanding Plastic Products
In general, there
are three elements of
an injection molded plastic part that need to be taken into account: wall
thickness, projections, and holes/recesses. These
will shape what type of mold is necessary as well its price and will at the
same time, influence the cost of the product. Click here to see more
about our mold making.
Inconsistent wall thicknesses
in an injection molded plastic part are one of the main causes of flawed
products. In designing the part, we aim to avoid excessively thick walls,
simply because thick walls use up more plastic and make the part more expensive. However, there is a limit as to how thin the part can be as well.
The strength of the part is a function of the thickness, and the final use
of the product will determine the desired strength.
Projections
are any aspects of the product that protrudes out from the
wall, such as reinforcement ribs. The ribs should no be thicker than the
wall or else risk that sink marks may appear.
Recesses and
holes are the last general design feature. The location of any
holes or recesses may significantly affect the product's overall strength.
Making holes in the side of any product can be achieved using slides in the
mold, however, it will increase both the cost of the mold as well as the
injection molding cost.
Hot Runner
Hot runner is another aspect regarding the mold/production that we have
expertise in. With a hot runner system included, you can eliminate sprues and runners, decreasing cycle time per part, improve
consistency in
the part, and allow for better control of the overall molding process.
Of course, this increases the cost of the mold, but we can discuss with you
whether this option is the best course of action for you.
Taking Care of Your Molds
We take special
care to properly store and maintain your injection molds in our possession
to protect your investment. If you own an otherwise
quality tool that
is producing less than satisfactory parts at a Chinese injection
molder, consider moving it to our factory to see the quality difference.
See more about our molds.
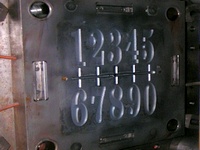 |
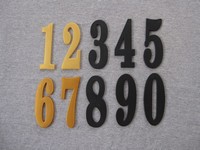 |
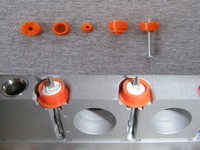 |
Mold for Numbers |
ABS Numbers in Black
and
Gold Pigments |
HDPE Caulking Cup |
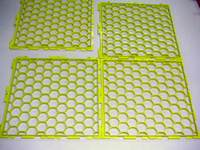 |
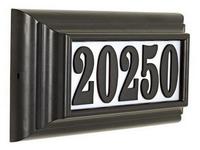 |
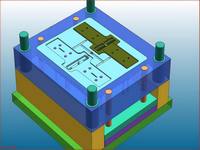 |
Engineered Plastic
Honeycombs |
Multi-Component
Lighted Address Plaques |
3D Molding Tooling
Drawings |
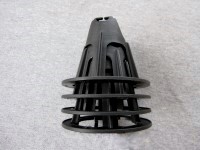 |
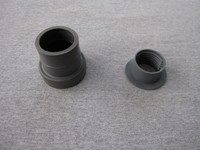 |
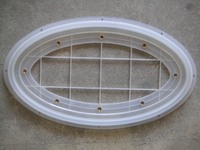 |
PP Rebar Chairs |
PVC (Synthetic
Rubber) Gaskets |
PE-LD
Insert Molded Frame Pattern |
Insert Molding
Insert molding is a process which uses injection molding to join separate
parts together into a single component. Click here to read
more.
Over Molding
Over molding is a
process that allows for two different molds to be used to injection mold the
same part in order to improve appearance or durability. Click here to
read more.
Rapid Prototyping
Rapid Prototypes are
very useful in checking form, function and appearance before spending large
amounts of time and money the production mold. Click here to read
more.
|
|