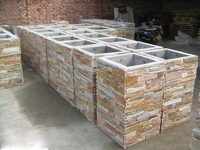
Stone Ledge Rock
Columns |
Home /
Mold Making /
Molds
All products
manufactured using all methods of manufacturing can obtain a
higher precision
as well increasing manufacturing cost-savings when using a mold to manufacture.
The quality of the mold is the most important factor in determining the
quality of your product but a good design is also critical. Our
in-house mold making department makes molds of all different types. We
have both the experience and expertise to make injection molds, die cast
molds, sand cast molds, pultrusion molds, extrusion molds as well as silicon
and gel coat molds (for hand layup). We also manufacture all of our
own fixtures and tools for assembly and testing.
Injection
Molds
Our design and
engineering team
takes into account the efficiency of the size of the mold as compared to how
many cavities it contains. 3c interglobal can also integrate the concepts of sliders,
ejector pins, inserts, mold materials and whether to use hot runners in determining your
mold.
A good design is
both critical and crucial and we maintain tight tolerances for every
dimension. All parts and molds are detailed in 2D assembly and
component drawings as well having 3D assembly drawings done. We prepare complete
documentation for tooling and manufacturing purposes to ensure proper assembly of
all components. Read more about our Injection
.
Molds usually take
30-60 days to complete, depending on many factors such as size, complexity
and mold material/hardness. For long-life production molds, we use
high quality tooling steel for our mold cavities, thus ensuring that the
mold is long lasting and can make hundreds of thousands of parts. Once
the first test shots are ready, we will courier them to you for
verification before production starts.
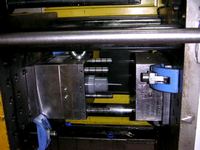 |
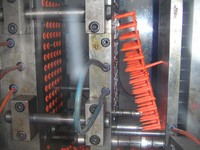 |
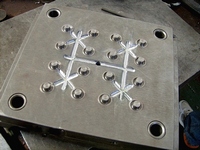 |
Mold for PVC Gasket |
72 Cavity Mold for an Assembly
Part |
Mold for PE-Low Density Bushings |
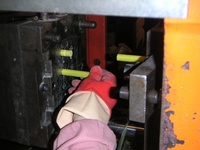 |
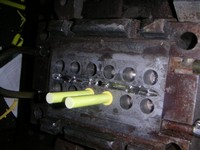 |
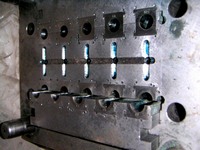 |
Insert Mold for High Tensile
Strength Pultruded Rods |
Mold is designed with removable
inserts for easy repair and durability. |
Prototype
Injection Molds
If you need to
produce a small production run, you can utilize a rapid prototype mold.
It will allow for full form, fit and function testing allowing you to see any
design flaws and also allow to you have a small market test before committing to a
production mold. While somewhat cheaper than a production mold, the
life of the mold is significantly reduced and may only produce a couple
thousand pieces.
Die
Casting Molds
Design team
at 3c interglobal analyzes your products for potential problem areas and concerns and
prepares a plan for the die casting mold. We
maintain just as tight a tolerance with our die casting as we do our injection
molding and our molds reflect that commitment.
Silicon Molds
Silicon and
Gelcoat Molds are both used in manufacturing FRP Composite products out of
hand
layup. With our silicon molds, we can replicate any finish and texture
and from our years
of experience have
created a proprietary process where we have precisely mirrored stone textures and finishes
on our FRP
Composite products.
With our gelcoat molds, we can create a mirror surface so that the product
manufactured from it has a the exact same mirror finish on the surface.
Read here for more information on Hand Layup.
Gel Coat Molds
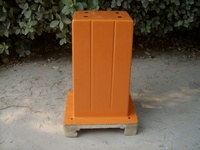 |
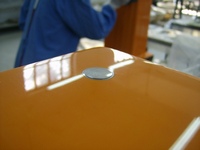 |
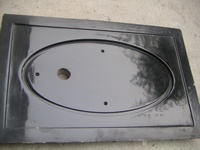 |
Mold for Mail Box |
We used air poppets to
de-mold the Mail Box |
Mold for Oval Frame |
|
|